research
Research fields
Atomization
The first investigated burner had a plain-jet airblast atomizer which allows an easy and flexible operation. In order to investigate the spray with a Phase Doppler Anemometer, we have started a collaboration with Jan Jedelský’s Spray Laboratory at Brno University of Technology. It became shortly evident that even this simple atomizer has numerous unknown features which lead us to deeper investigations.
Firstly, the Sauter Mean Diameter was analyzed and by the measurements, the predictive formulae available in the literature were extended to the high-velocity atomization regime. Following the thread, the effect of liquid properties and liquid preheating were investigated and published.
Currently, we are focusing on the turbulent characteristics, spray cone angle, and statistical analysis of the spray.
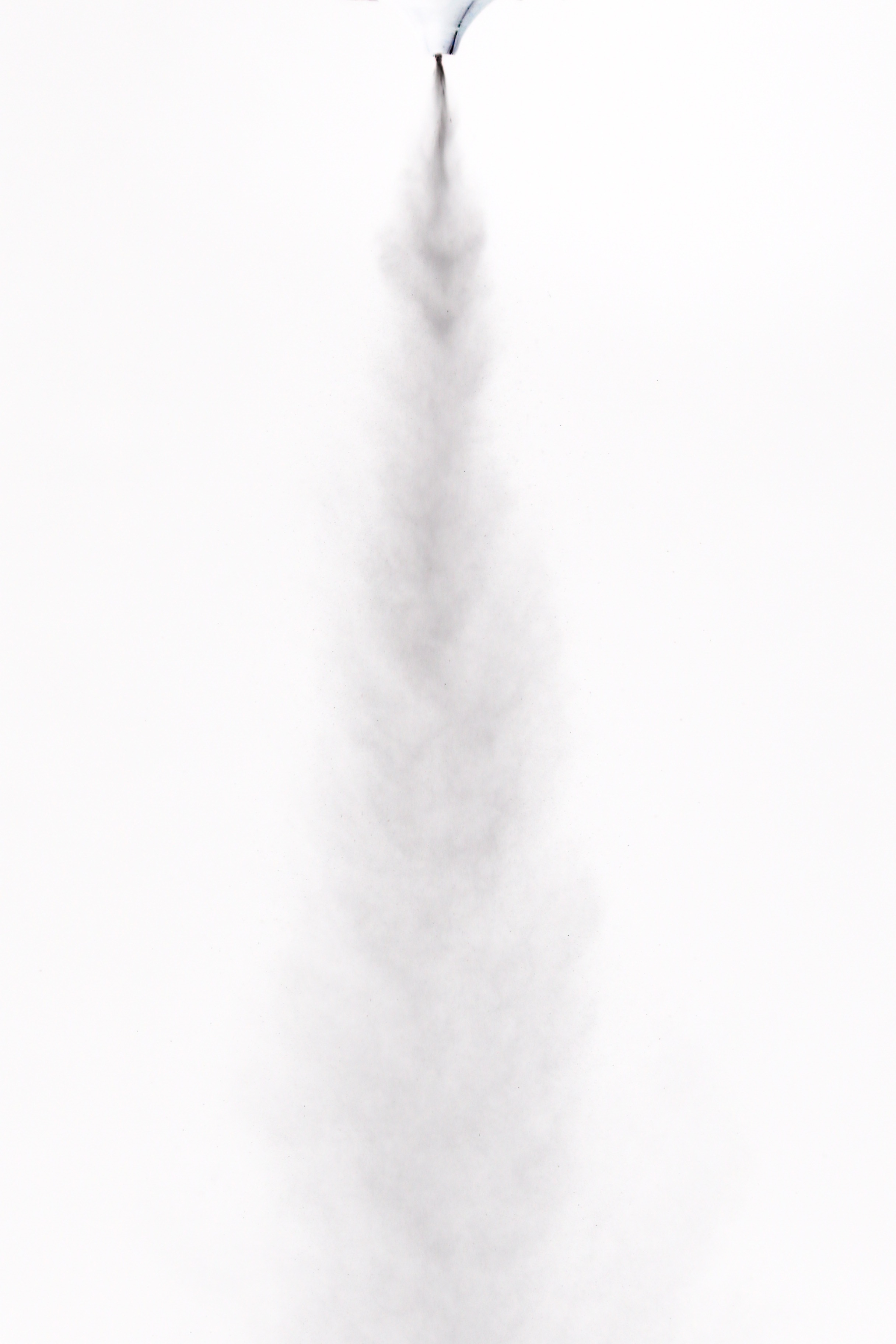
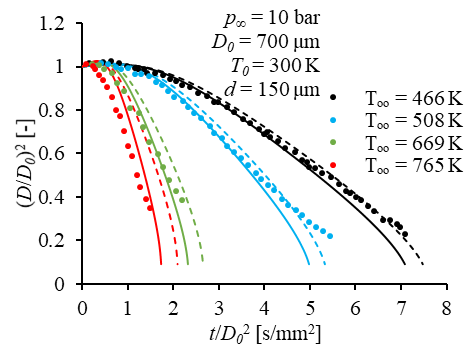
Evaporation
If atomization is complete, liquid fuels need to be evaporated to mix the fuel vapor with air which is a prerequisite of stable, low emission combustion. The challenges are twofold. Firstly, establishing a reliable evaporation model needs reliable measurement data. However, this is only available for droplets of few hundred um in diameter while practical fuel sprays feature a magnitude lower droplet diameters.
Secondly, a reliable material property database is necessary to complete the calculations. These feature common data like liquid density and specific heat alongside more exotic properties like vapor heat conductivity and vapor dynamic viscosity.
By handling the two fields together, better evaporation estimation can be performed with advanced models. To evaluate the quality of different models, distillation measurements are performed.
Diagnostics
Modern emission standards push combustion to its edges where even the steady flames require transient treating since the operation becomes quasi-steady. This is lean turbulent swirl combustion, a concept that is several decades old while it still bears several unknown phenomena which are even more complicated with liquid fuels.
Recent data acquisition systems provide the necessary environment to analyze and control several parameters from which pressure and light time series correlate excellently with the governing physics. These two signals give a robust evaluation platform for combustion stability evaluation. Their correlation with pollutant emission measurements makes a powerful tool for dynamic operation while pollutant emission must be low all the time.
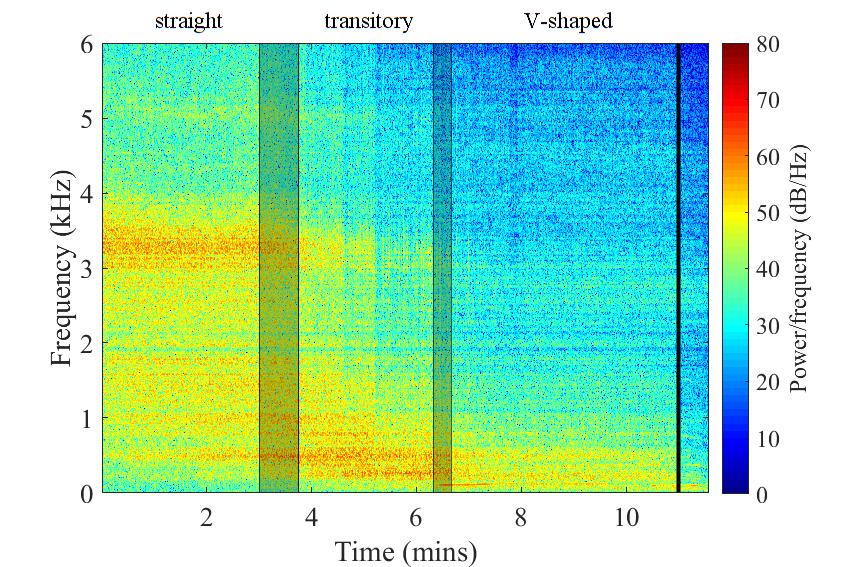
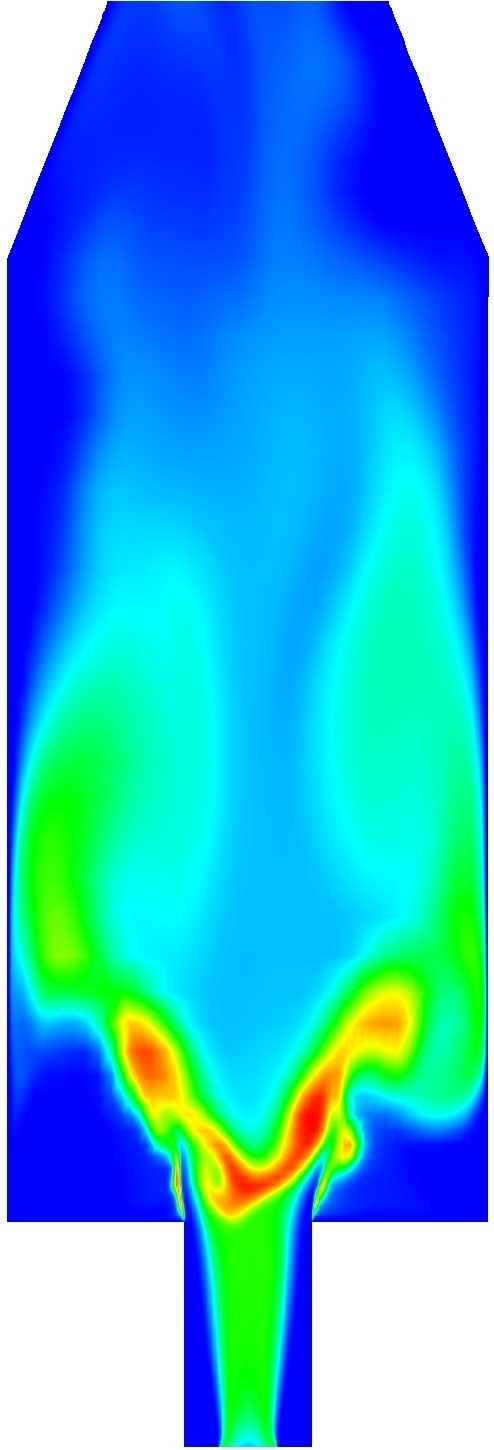
Numerical simulation
Combustion research is mostly experimental even today. The answer for this is the complex coupling between reaction kinetics, fluid mechanics, and thermodynamics. The majority of the difficulties rise when one starts implementing detailed mechanisms to multi million cells since computational power skyrockets even for a hydrogen-oxygen system which is significantly simpler than any practical fuel.
In a real combustion chamber, the problems are rarely related to reaction kinetics, meaning that the fuel and the oxidizer may mix and combust perfectly in most cases. The inefficient operation primarily originates from the faults in flow patterns which are actually worth the effort to simulate.
Presently, CFD is used for evaluating the design of the new test rig and improve the combustion characteristics. In later phases of the research, various fuels and conditions, new concepts will be tested prior to its application.