Numerical simulation
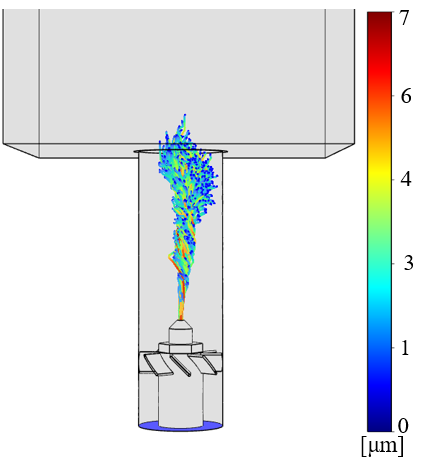
Mission
Our goal with numerical modeling is to perform calculations using tabulated chemistry models, which are simple and robust enough for industrial applications, evaluating liquid and gaseous fuel combustion. The real burner geometries are modeled with poly-hexcore cells. Atomization and evaporation of liquids are modeled in the Lagrangian frame. In this framework, a few hundred thousand cells and simplified models match the global flame characteristic. Also, pollutant emissions are evaluated. We are using principally the ANSYS Fluent software environment, the leading commercial CFD software.
Swirl vanes
The Mixture Temperature Controlled combustion concept notably differs from the known flames in the literature. Therefore, its simulation is a principal goal to understand its operation better. Since the burner geometry is highly modular, modifications can be estimated in advance to optimize the design. These parts include nozzles for gaseous and liquid fuels, swirl vanes, and combustion chamber geometry. A highlighted project is the evaluation of swirl vanes, hence the effect of vane angle. This analysis was initiated for natural gas combustion within the framework of a student project. The validations were performed by flame photos, Schlieren images, and NOx and CO emissions at 45° vane angle.

Ammonia combustion modeling
Ammonia is a carbon-neutral energy carrier. Before direct application in boilers and gas turbines, its simulation is inevitable. Hence, in 2021, in cooperation with an MSc student, pure ammonia combustion was simulated in our lean premixed swirl burner system. It was found that the Flamelet Generated Model is appropriate for the simulation using Okafor’s reaction mechanism even near the lower flammability limit. The main problem of the combustion of pure ammonia is the huge NOx emission. Hence, we started collaborating with researchers of the Shanghai Jiao Tong University, who provided PIV data of their lean premixed swirl burner. During the simulation, Okafor’s ammonia-methane combustion mechanism was applied, and non-adiabatic flamelet generation model was used. The results were validated by PIV and OH* chemiluminescence measurements, showing a good match.
Mixture Temperature Controlled combustion modeling
Modeling of the resulting distributed combustion modeling was performed for diesel fuel by using the Flamelet Genereted Manifold model, and tweaking the parameters of Zimont turbulence model to decrease the turbulent flame speed and delay the ignition, well matching with Schlieren measurements, pollutant emissions, and acoustic spectra. The results bear high potential for the industry to design their own MTC combustion systems for stable, reliable, and environmentally friendly operation.
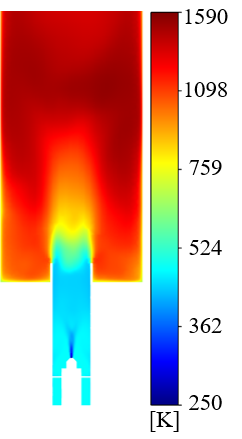